CAPA Software | What are the major functions of CAPA Management Software ?
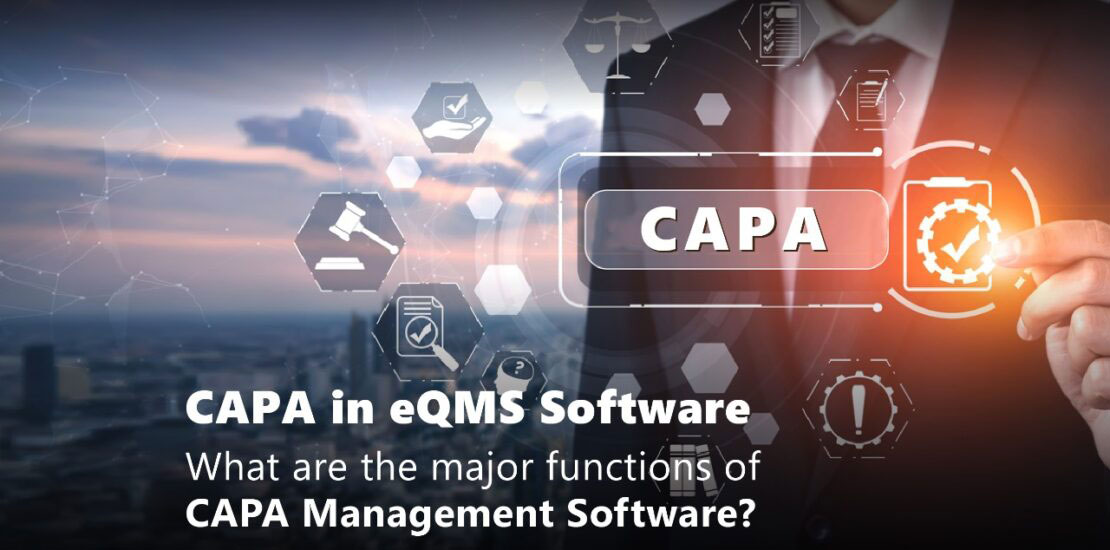
Article Context:
In the Quality Management of the life sciences industry, CAPA is a more crucial compliance threat than any other as it is a trigger for FDA-related regulatory warnings – 21 CFR Part 11 Compliance. Therefore, life science industries do require a software – electronic Quality Management System (eQMS) with robust automation to manage FDA-regulated validation process requirements of CAPA (Corrective Actions and Preventive Actions) and NC (Non-Conformances).
It is not that the FDA-regulated organizations with an eQMS – CAPA Management Software in place don’t receive a warning letter. They do receive compliance-related warning letters about the failure of the eQMS system for one or more reasons. When choosing software, ensure that you know the essential functions of eQMS – CAPA capabilities to significantly reduce regulatory risk and quality risk belittling brand reputation and threatening patient safety when choosing the right eQMS solution.
Below listed are some of the capabilities that your eQMS system should own to avoid the risk of Part 11 FDA-regulated non-compliance.
Must-Have Functions of eQMS – CAPA Management Software:
eQMS Software (electronic quality management software) is a technological innovation designed and developed to automate quality processes and reduce the regulatory risk associated with quality issues while safeguarding life science companies from FDA-related compliance risks. CAPA is a quality event that is integrated as a module within the eQMS in coordination with non-conformance, complaints, change control, document management system, and training management system.
CAPA is an essential element in a quality management system when the organization wants to identify, investigate and resolve quality-related issues in adherence to the FDA.
Purpose of CAPA System
- To record and analyze information to identify the potential quality problems.
- To investigate the root cause of the quality issue and implement appropriate and effective corrective or preventive action.
- To validate the implemented corrective and preventive actions.
- To assign the implementation plan to the appropriate people.
- To provide information for management review.
- To document activities and processes.
- To be compliant.
In an eQMS, the CAPA system capabilities are as follows:
- Must include CAPA processes and procedures that an organization follows
- Data analysis and insights in identifying the CAPA root causes and quality issue sources.
- Help organizations implement and monitor corrective and preventive actions.
- Integrate and communicate with other systems like document management system, change control, non-conformance, and training management system, ensuring data security and quality.
- Facilitate organizations to focus on overdue or past due CAPA records and formal failure investigations
- Allow organizations to validate the effectiveness of laid corrective and preventive actions.
Though the above said are essential requirements, they don’t translate to how effectively a CAPA system will function and don’t help you in picking the right software for your organization. Consider the following eight essential functions when choosing an eQMS – CAPA system.
Report the issue
The eQMS should have the feasibility to report the CAPA and document the corrective and preventive actions taken. This can be a standard template, but a configurable one will help the company to follow the process of inputting the data without a change. The standard CAPA template should hold the details as follows.
- Issue title
- Issue occurred date
- Issue description
- Issue raised by
- Issue assigned to
- Root cause analysis
- Implementation of Corrective Actions and Preventive Actions
- Planned resolution date
- Actual resolution date
Documenting the above information is basic to comply with FDA regulations and CGMP requirements. Ineffective reporting of issues and ineffective documentation are the critical factors of CAPA system failure in an organization. If your CAPA system allows you to document the information just as in spreadsheets or documents, the issues will never be resolved and will become expensive quality regulatory concerns. In addition to supporting the input of information, if the system offers coordination and collaboration of information across the organization with auto-saving functionality can help users with the required insights for laying corrective and preventive actions. The CAPA system should be capable of handling small issues/deviations as Non-Conformances and the issue that require proactive resolutions as CAPAs.
Integrate seamlessly
If a CAPA system doesn’t integrate seamlessly with other quality applications or is not a part of comprehensive quality management software, then there is no scope for exploring automation which could lead to data quality risks and eventually lose organization-wide visibility. Integration of the CAPA system with supporting quality systems can lead to process improvements, such as triggering an SOP (Standard Operating Procedures) document change with document change control, assigning implementation and effectiveness check tasks to employees across the globe, eliminating data entry errors, resolving quality issues swiftly, and monitoring and tracking closed-loop trends.
Intuitive forms
The CAPA system should add value to your organization by driving the user to use it for its purpose by introducing automation making the user’s job easier. The system should validate the information entered to its accuracy and help the user to fill in the information that is left out unknowingly. The data entered should be presented in a meaningful and logical way boosting the completion rates and reducing user effort and errors streamlining the organization’s quality operations. With this context at a high level, the CAPA system capabilities include
- Cloud storage of files, data segregation, and storage
- Web-based templates, edit online, and workflow tracker with a reviewal and approval process
- FDA – 21 CFR Part 11 Compliant Electronic Signatures and Non-editable audit logs with user details and time stamps.
Quality processes linking
The organization can drive better improvements in quality processes when the CAPA is a module of eQMS rather than a standalone application. The CAPA system, when standalone, will only allow the organization to raise and resolve the capa issue proactively and forget about the issue in the near future. But when the CAPA system is a module in a QMS (Quality Management System) and actively communicates with other quality processes like the document management system, training management system, complaints, change control, etc. can lead to effective root cause investigations and drive better quality improvements in terms of processes and procedures followed. Additionally, with quality processes linking, a CAPA can be triggered from an NC when proactive resolutions are needed, which in turn can trigger a process training with a specific set of users, reducing manual efforts.
Reminders and notifications
With the globally distributed teams and being a centralized quality system, your CAPA Software should not allow the user to forget or deviate from the issue resolutions with time. The CAPA system should have the capability to avoid unnecessary long email trails for issue updates and remind users of actions on issue resolution. An efficient CAPA system helps collaborate and automate the process of issue resolution by assigning tasks to the right people at the right time, notification of tasks, auto reminders, and cloud-based and role-based access.
Workflow tracker
The FDA warning letters are the result of process inconsistency. When CAPA is known as a critical issue, organizations don’t tend to forget or neglect it. The users just lose track to complete the process cycle effectively. To do so, your CAPA System should guide the users through a step-by-step process to close the issues on time through a streamlined process and quality processes linking for effective closure of issues.
Auto filling of data
When there is a process linkage, like a complaint requiring a preventive action or a non-conformance requiring a proactive resolution for the issue to not occur in the future, and if the user depends on manual entry of data can lead to risky data issues and inconsistency of data across the organization. If the system can auto-fill the data from a complaint or non-conformance when a quality event is triggered by, providing automated inputs from the linked quality systems will help the organization to perform an effective analysis of trends at a prominent level.
Non-editable audit trail
While evaluating an eQMS with a CAPA module, opt for the system that provides detailed audit trails. Be it a CAPA or NC or any quality event, in that case, to avoid FDA compliance issues and to be regulated by meeting the ISO and FDA standards, the non-editable audit trail is a must to have to support data-driven management. The system should capture the entries when a quality event is created, edited, updated, and when moved from one workflow state to another and should be kept secured as long as the electronic quality records are stored. Each entry should be attributed to the person who made changes or was directly involved in record creation or edition, and the time stamp of when and why the changes are covered.
In conclusion
The CAPA system is the foremost critical solution for FDA-regulated life science industries. A compliant, product-centric Quality Management System with CAPA capabilities helps organizations to avoid 21 CFR Part 11 – FDA compliance related to quality issues. Being in the life sciences industry, maintaining regulations and compliance will be easier with less anxiety, risk, and overhead. Hence while choosing an eQMS, opt for the one which is specially designed with automation factors for small to mid-sized companies and avoid regulatory risk by considering proactive approaches to resolve quality events.
Schedule a demo with us if you are looking for an effective CAPA Management Software with the above-mentioned essential functions.
FAQ's
How do you measure the effectiveness of CAPA in CAPA Software?
The effectiveness of the CAPA is best measured using both qualitative and quantitative data. The qualitative data will aid in gaining insights into the problem and determining root causes, as well as understanding the problem and its resolution. Quantitative data, such as numerical data collection and predictive hypotheses, will aid in predicting issues in the near future and/or assessing effectiveness.
What is the purpose of a CAPA Software?
The purpose of the CAPA Software is to correct and prevent defects or issues within the company. Corrective action is determined based on the investigation process for the non-conformity that occurred. In contrast, by analyzing the risk threshold, preventive measure is planned to prevent the same problem or non-conformity in the future.
What should a CAPA Software include?
A CAPA Software includes:
- Identifying and investigating existing and potential quality issues
- Identifying the actions needed to resolve and correct the problems and to prevent their recurrences
- Verifying the corrective actions implemented are effective
- Implementing changes in procedure
- Disseminating information about the quality problems
- Submitting the report for management review
How to improve CAPA Process in CAPA Management Software?
- To start with improving the CAPA Process, organizations need to perform an in-depth analysis of the root cause to investigate the actual cause of the problem. To do so, identify the problem, define the issue that occurred, understand the sources, examine the process and identify the potential root cause.
- After investigating the root cause, get the stakeholders involved and document the investigative information to ensure the determined actions are implemented and executed for resolutions.
- Focus on Corrective action to eliminate the problem and Preventive measures to eradicate the same problem in the future.
- Adopt an automated quality management system to streamline the CAPA process and focus on the correct issues that matter most with the AI-enabled reports and stats. Also, keep track of the process progresses, saving resources and time.