CAPA PROCESS – STEP-BY-STEP INSTRUCTIONS
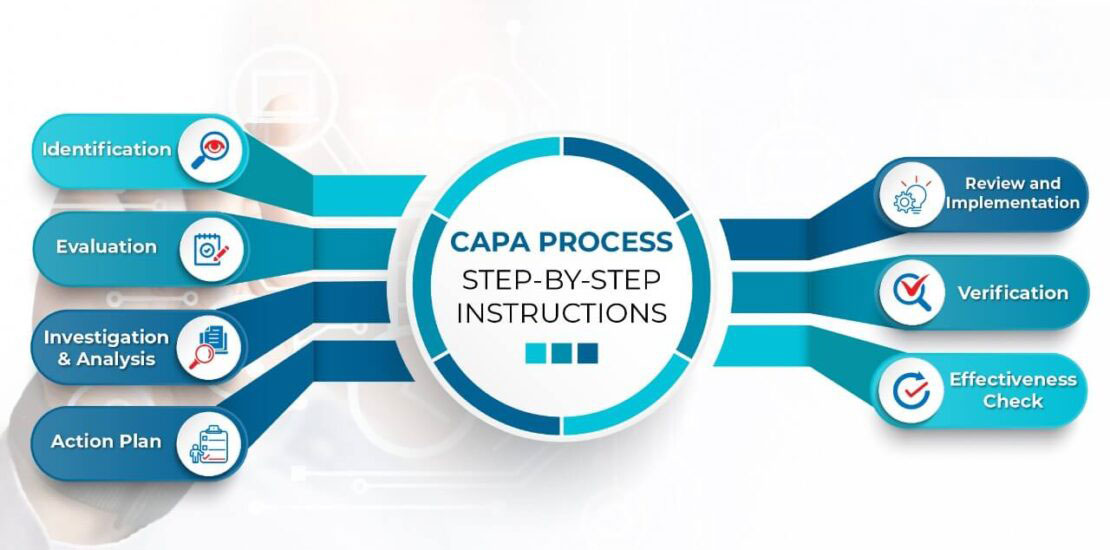
Article Context:
Corrective And Preventive Action (CAPA) is often discussed as it is an alarming issue for the life sciences industry. Organizations consider its importance and try to deal with it better as CAPA‘s are the key indicators of a process that investigates the problems, identifies the source, solves the issue with corrective actions, and prevents its reoccurrences by preventive measures. Any flaws in the process would lead to FDA (Food and Drug Administration) warning letters and compliance grievances.
So, Quality Management System has produced a step-by-step process to help companies handle the CAPA process to get satisfactory results in adherence to ISO (International Standards Organization) FDA regulations.
Every problem cannot be a CAPA and cannot ignore a minor NC (Non-Conformance), leading to a systematic issue. QMS (Quality Management System) will make you define, manage, and implement an effective CAPA process meeting the regulation requirements for a quality management system. A proper and effective CAPA process is proof of an effective quality system of an organization and speaks about the safety and quality measures followed by the production staff.
CAPA PROCESS STEPS
The CAPA process comprises seven steps as highlighted below.
Step-by-step risk-based CAPA process
- Identification
- Evaluation
- Investigation & Analysis
- Action Plan
- Review and Implementation
- Verification
- Effectiveness Check
Identification
1. Identify a systemic issue
Identify the systematic issue, document it, creating a CAPA record in Quality Management System. The CAPA source can be a customer complaint, internal or external audit inspection, Non-Conformance, or process or procedure deviation identified by the employee.
2. Raise a request to create a CAPA
The initial step starts with elaborating an issue, followed by detailed information, including the source and evidence. With the evidence, the CAPA record creation becomes valid for evaluation and approval. Finally, the CAPA gets created with an identification number allotted automatically by the QMS that helps keep track of the CAPA process.
Evaluation
3. Review the CAPA request to formalize it in the system
QRB (Quality Review Board) in an organization evaluates the documented issues to assess their appropriateness and determine the need for action. Then, based on the potential impact of the issue raised for the staff, the created request gets formalized by the system’s quality assurance team. Hence, the identification process holds the detailed information to estimate the problem scrutiny for this step.
4. Accept or Reject the CAPA request process
The next step is the created request. With the information of understanding, the quality analyst, or the member in charge of the review team will analyze the need for action. Based on the findings of the issue identified, the request can be rejected or accepted. If rejected, document the reasons determining the facts for rejection. If accepted, the CAPA process gets initiated.
Rejection or Acceptance of CAPA requests is configured in the QMS and authenticated with E-Signatures. In addition, every edit gets recorded electronically in QMS as non-editable audit logs. The E-Signatures and non-editable audit logs adhere to 21 CFR (Code of Federal Regulations) Part 11 Compliance of FDA and ISO.
5. Requested CAPA gets into the process
The assigned identification number helps to track the CAPA process. From this step, it is essential to overlook the process and the workflow states. The Quality Management System supports a path of progress with clear audit trails describing the changes and edits in detail, making it available for inspection with just a click when required. The process is quite impossible on a paper-based process as there is a high chance of misplaced or missing information and improper tracking of the CAPA process. However, the process is crucial as many companies have received warning letters from the regulatory board for improper or failed CAPA process tracking and for CAPA being open for an indefinite period.
Investigation & Analysis
6. Ensure the CAPA information is accurate
The information added into the system must include all information about the product, process, or issue contributing to the CAPA to ensure the investigation is completed and determine the appropriate action plan.
7. Investigate and record the findings
The identification of CAPA source strengthens the investigation findings. The investigation might need collaboration with multiple teams like the engineering team, manufacturing, product delivered, or even the raw material supplier to get to the when, how, and why.
8. Root Cause Analysis
With the investigated information, determine the root cause of the issue. People make mistakes by jumping on this step before collecting the required and relevant information. Without the facts and proof, root cause determination is impossible. Users should know the factors that have contributed to the occurrence of the issue. This step involved rigorous investigation, documenting the information, and analyzing the data to determine the root cause of the problem for creating a Corrective Action.
The lack of documentation of investigation information or failure to reach the root cause of the issue may result in a wrong analysis that fails to fix the problem at hand, resulting in CAPA being open for a definite period.
The QMS (Quality Management System) has configurable RCA (Root Cause Analysis) tools in line with the organization process. The most prominent and efficient RCA is 5 Why’s, where one question will lead to the other in sequence, drilling down to the root cause of the issue leading to its countermeasure that helps prevent the problem from recurring.
Action Plan – CAR (Corrective Action Request) & PAR (Preventive Action Request)
9. Determine an Action Plan
With the RCA technique, define the action plan and document it for reviewal and approval. Ensure the action plan lists out the required action plan in the process or procedure or system specifications or manufacturing changes etc., to control and correct the issue and help determine preventive actions to prevent the recurring problem.
10. Complete the Action Plan
To achieve the desired results, document the action plan and assign roles for execution. The following are some examples of corrective action plan executions.
- Update the procedures or process methods
- Redesign a product specification or design
- Add audits to check for accuracy
- Implement additional training plans for the users working on the specification
- Switch raw materials or suppliers
- Policy or guideline change
Review And Implementation
11. Review the CAPA process
The quality team will review the CAPA process for completion based on the documented information checking for its accuracy. Finally, the QRB analyzes the action plan based on the risk thresholds.
12. Approve or Reject CAPA Action Plan
The approver reviews the investigation analysis and the written action plan, approve it by e-signing and makes it available to all stakeholders to implement the corrective actions. In case of rejection, the QMS provisions the Quality Manager/Approver to document the rejection comments for audits.
With Quality Management System, companies can have records available for audits or inspections at fingertips without the need to dig through files, search relevant papers to show the CAPA progress. QMS (Quality Management System) ensures your CAPA process progressed in the right path providing end-to-end visibility and traceability of the process handled.
13. Implement the Corrective Actions
Corrective actions, as the name suggests, the measures defined are to correct the issue at hand. So, it is essential to carry them out promptly as defined in the process. Corrective actions cannot be permanent resolutions to the problem. To implement the best laid disciplinary action, systematic issue identification and investigation of the root causes play a key role in correcting the problem. Corrective action plans often include redesigning the product, fine-tuning the instrument calibration, or process modification etc.
14. Implementing the Preventive Actions
As the name implies, preventive actions are prediction-based proactive measures implemented to prevent the problem from recurring or monitor the potential risk to escalate into a significant or harmful issue.
Common Preventive measures are
- Conducting risk assessments
- Regular performance checks
- Implementing training programs
- Deviation check plans
- Regular internal audits
Verification
15. Verify CAPA Resolution
Verify the implemented CAR and PAR, monitor and document its effectiveness or ineffectiveness. Ensure that the Corrective and Preventive actions defined are effective, add additional changes, if required, in understanding the CAPA actions formalizing the CAPA process completion.
Effectiveness Check
16. Efficiancy of actions
The effectiveness check is the last and vital step in the CAPA process as it ensures the actions defined are appropriate, resolves the issue, and prevents its recurrence. There are diverse ways to determine the effectiveness check based on the measures implemented. For instance: analyzing human errors, checking for deviations before and after implementation of CAR, surprise internal audits to check for the process, machinery, and employee performance.
COMPLIANCE AND CREDIBILITY
The critical reason for managing and streamlining the CAPA process is adherence to FDA and ISO regulations. To reassure the FDA and be compliant with the rules, document every action of the CAPA process from the start to end, from the issue identification to resolution. Because the CAPA process assesses the quality issues, it corrects and prevents them from recurring.
The proper documentation of the CAPA process itself speaks about effective and efficient quality processes in an organization. Moreover, it gives the needed credibility for the companies to operate in the Life Sciences industry.
To conclude,
Managing a CAPA process on paper is incredibly challenging. Documenting the entire process is impossible and achieving full traceability and visibility is a dream because each CAPA can be at a different workflow state.
Compliance Group QMS Software helps companies document CAPA, record the process flow, and make it available seamlessly. QMS provides traceability and visibility of issues and helps connect similar patterns in the system with a holistic view of quality issues. In addition, the critical data is presented visually, enhancing decision-making with relevant insights that might take long hours on a paper-based system.
FAQ's
What is the first step in the CAPA process?
CAPA stands for Corrective and Preventive Action. The first step in the CAPA process is to identify the source of the CAPA and to determine the root cause or underlying cause of the CAPA initiation. This is not a one-step process; it also necessitates a collaborative effort to identify the potential cause of CAPA. A CAPA may have multiple root causes at times.
What is CAPA verification?
The CAPA verification process entails verifying and monitoring the effectiveness of the implemented CAR (corrective action) and PAR (preventive action). Documenting the effectiveness check results ensures that the Corrective and Preventive actions defined are in accordance with the process, and make any necessary changes in order to formalize the completion of the CAPA process.
What is the CAPA format?
A CAPA format is a template that is intended to assist the quality team members in identifying, investigating, verifying, and implementing the CAR and PAR to resolve the issues and reduce the likelihood of occurrences adhering to regulatory standards.
What is CAPA root cause analysis?
The Root Cause Analysis is the most important step in the CAPA Process because defining and implementing CAR and PAR measures to resolve and prevent the issue is nearly impossible unless the underlying cause of the problem is identified. In layman’s terms, the root cause is the sequence of events that leads to the occurrence of a problem.