CG MAKES VALIDATION DIGITAL, EASIER, FASTER, AND SMARTER
CG helps clients implement the right processes and systems to streamline the complex methods of process validation. Our proven process validation flow chart keeps everyone aligned and collaborating to ensure patient safety and product quality.
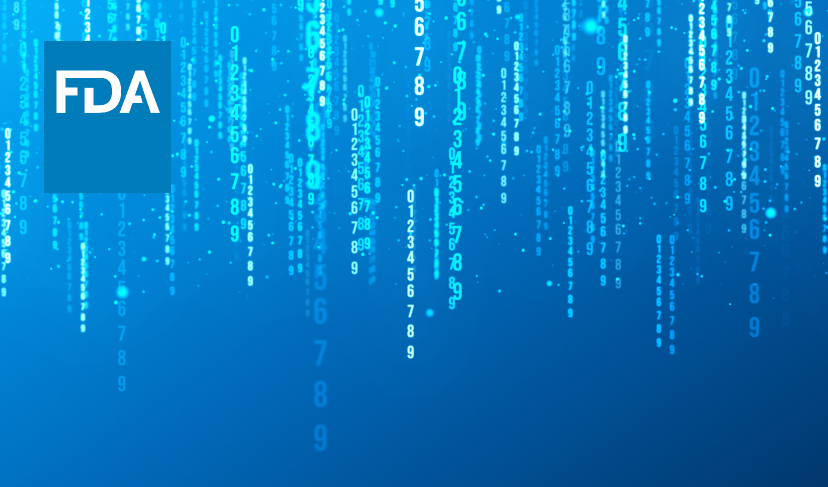
WHITEPAPER
What Does Process validation Mean to the FDA?
The FDA defines process Validation as “the collection and evaluation of data, from the process design stage through commercial production, which establishes evidence that a process is capable of consistently delivering quality product.”
CG HELPS CLIENTS TACKLE THE COMPLEXITY OF PROCESS VALIDATION REQUIREMENTS
In the simplest terms, Process Validation is the exercise of confirming manufacturing capabilities consistently to reliably produce a product that meets intended requirements. The FDA, ISO, GHTF, and others have released guidance documents to help clarify the minimum requirements for Process Validation. Despite the significant amount of content available to the industry, organizations often struggle to conceptualize implementing a holistic validation approach – and wait until they receive major findings from auditors to align with federal regulations.
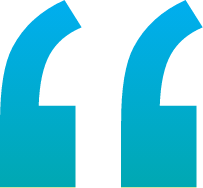
Partnering with CG on our manufacturing changes and process validation has been a transformative experience. Their meticulous approach, tailored solutions, attention to detail and industry expertise have not only ensured regulatory compliance but also streamlined and optimized our manufacturing processes. The seamless collaboration has significantly enhanced our overall product quality. Choosing CG is an investment in quality and regulatory excellence.
– Director of Process Validation, Prominent Global Pharma Group
THREE CRITICAL PHASES OF PROCESS VALIDATION
Process Design
The underlying goal during a Design of Experiment (DOE) study is to iterate the process to the point where the critical process parameters (CPPs) are identified, characterized, and optimized.
Process Qualification
During the process Operational Qualification, the engineering team tests the limits of the processes with “worst-case” conditions and establishes the nominal settings to be tested during the process Performance Qualification.
Continued Process Verification
Continued Process Verification is the consistent monitoring and evolution of process performance to ensure that the manufacturing operations for the product remain in a state of control.