Process Validation | US FDA Medical Device Validation Process | Why it’s Important?
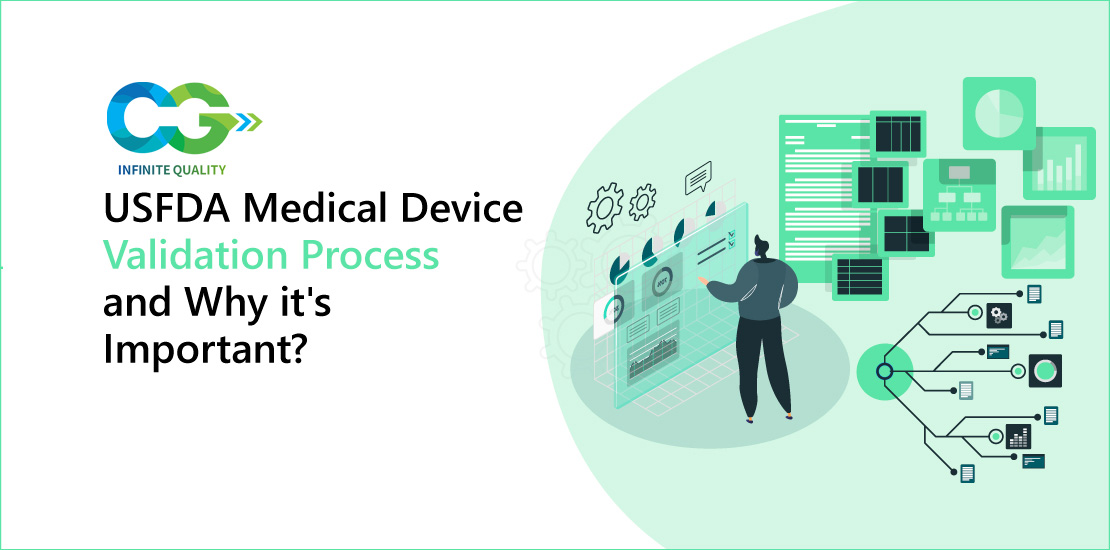
Article Context:
- Importance of USFDA Process
- Process for Device Validation
- Validation and Verification of Medical Devices
- Significance of Process Validation for the manufacturers of Medical Devices
Importance of USFDA Process
The US Food and Drug Administration (FDA) is responsible for protecting public health by ensuring medical devices’ safety, efficacy, and quality. The agency has developed a rigorous medical device validation process to do this.
The process begins by submitting a device for premarket review (PMR). It is the first step in the validation process and is always used to check if the device is safe and effective. If the device passes the PMR, it can proceed to clinical trials. After clinical trials, the device is safe and effective; it can be approved for production and then into the market.
Process for Device Validation
Device validation is essential because it ensures that medical devices are of the best standards and quality with no malfunctioning of any sort.
The Validation Process for USFDA Medical Device applications can be pretty complex and time-consuming. The first step in the validation process is to apply USFDA. After an application is submitted, USFDA to determine if it is complete. If the application is incomplete, USFDA will request additional information from the applicant. Once the application is complete, USFDA will conduct an initial review to determine if it meets the eligibility requirements for approval. If the application is eligible for a license, USFDA will conduct a full assessment to determine if the device is safe and effective. If the application is not suitable for approval, USFDA will provide the applicant with a reason for the rejection.
Medical devices are essential to the quality of life of patients. However, because medical devices are complex, there is a risk that they will not work as intended. For effective and safe medical devices, proper validation is necessary.
Validation is a process used to determine the accuracy, reliability, and validity of a product or system. The goal of validation is to ensure that a product is effective and safe. Validating a medical device involves testing it to determine how it works in the real world.
There are several ways to validate a medical device before getting it in the real world. An essential way of validating is through a controlled environment in a lab.
Validation and Verification of Medical Devices
While validation is verifying that a medical device is safe and effective, Device verification is proving that a medical device meets specific requirements. Once a medical device is validated, we can send it to the market. However, it is essential to understand that validation does not guarantee that a medical device is perfect.
Significance of Process Validation for the manufacturers of Medical Devices
There are said guidelines and processes that the manufacturer has to follow. The Process validation guidance for manufacturers can help ensure manufacturing processes’ accuracy, consistency, and reliability. Validating a manufacturing process can help ensure that products are produced consistently and meet specifications.
Manufacturers can use various methods to validate a manufacturing process, including process mapping, verification, validation testing, and process improvement. Process structure and mapping can help manufacturers understand the steps involved in a manufacturing process and identify areas that may need improvement. Process verification can help identify whether a process operates as intended and ensure that products meet specifications. Process validation testing can determine whether products meet specific performance criteria and ensure the accuracy of a process. Process improvement can help improve the efficiency.
FAQ's
What is the difference between process validation and Performance Qualification?
Validation is an action, procedure, or instance that supports or collaborates with something on the basis of solid, reliable evidence. Establishing the authenticity or reality of any kind is termed verification. To ensure that something complies with a condition, standard, and other requirements, something also must be qualified.
Why do you need 3 batches for validation?
The justification for choosing three batches is that quality issues could accidentally be introduced into the first batch of products during manufacture.
Second batch manufacturing quality could be typical.
It ensures validation or quality of the third batch provides us confidence that our method is validated if the same quality is attained in the third batch, which signifies that our results are consistent and reproducible.
If the desired quality criteria are met in the first batch, this may be considered an event, the same quality may be met in the second batch by coincidence, and the same quality may be met in the third batch by consistency.
What is difference between CPP and CQA?
The term “critical process parameter” (CPP) is used in the pharmaceutical industry to refer to process variables that affect a critical quality attribute (CQA) and should be tracked or regulated to ensure the medical product meets the required standards for quality.
The criticality of a quality attribute is essentially determined by the severity of the harm, and it is unaffected by risk management. The impact of a process parameter on any crucial quality aspect is related with the parameter’s criticality.
How many batches are needed for process validation under the new FDA guidance?
The usual argument for choosing three batches is that quality issues could accidentally be introduced into the first batch of products during manufacture.
Second batch manufacturing quality could be typical.It ensures validation or quality of the third batch provides us confidence that our method is validated if the same quality is attained in the third batch, which signifies that our results are consistent and reproducible.
If the desired quality criteria are met in the first batch, this may be considered an event, the same quality may be met in the second batch by coincidence, and the same quality may be met in the third batch by consistency.
What is process validation in medical device manufacturing?
Process validation is the process of proving by unbiased evidence that a process regularly yields a result or product that satisfies its predefined requirements.
The process must be validated with a high degree of assurance and approved in accordance with established protocols when the results of a process cannot be fully verified by subsequent inspection and test. The validation processes and outcomes, as well as the date and signature of the person or people who approved the validation and, if applicable, the major equipment validated, must be documented.
What are the 4 types of validation?
- Prospective
- Retrospective
- Concurrent
- Revalidation
What is validation protocol in pharma?
A documented plan outlining the process that has to be validated, along with the production machinery that will be used, is known as a validation protocol. The precise elements and actions that will make up a cleaning validation study must be defined in a validation protocol.