Digital Twin Manufacturing: Your Sidekick for Maintaining the Validated State
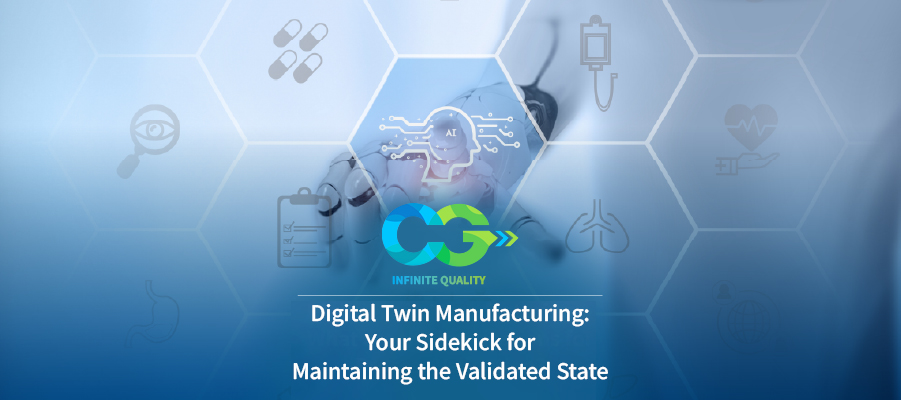
Article Context:
Envision a not-so-distant future, when logging into your computer opens the door to an instantaneous digital replica of your company's manufacturing line. In this virtual world, a constant stream of real-time data on production key-performance indicators (KPIs) feeds into your model. With access to this simulated environment, you have the power to make dynamic modifications and resolve critical issues—without any immediate repercussions on real-world manufacturing. Confirmation bias is now out of the picture for changes. Instead of spending precious time planning various combinations of production processes, you’re able to now simulate hundreds, if not thousands, of iterations per day. With this superpower, making changes to the validated state is no longer mere guesswork; it’s a well-supported decision backed by ample data. This innovative technology may be reminiscent of the tools carried by heroes like Batman or Iron Man, but this is no longer something you’d see only in the movies, it’s happening in real life. So, the question is: Are you ready to join the New Avengers?
How does Digital Twin Technology work?
Digital Twin Technology utilizes AI and IoT (Internet of Things) devices and sensors placed on physical objects to scan and collect data. That data creates a visual representation of the objects that were scanned. For example, an entire Factory floor containing hundreds of materials and machines can be displayed virtually. The technology sifts through historical data and analytics to make predictions and provide insights for efficiency and optimization. The AI within is constantly learning and growing with each day, so it will always stay ahead and updated, ready for any new challenges it may encounter.
Benefits of Digital Twin Technology in Manufacturing
In a world full of production inefficiencies and challenges, a supernatural tool emerges from the shadows, granting its users various powers needed to save the day. Armed with Digital Twin technology, Validation and Verification efforts are simplified. Revolutionizing the Manufacturing battlefield, factories can adopt a seamless transition to become more efficient, optimized, and sustainable.
Predictive Maintenance
With Digital Twin Technology, you have the power to see into the future to prevent issues before they happen. Manufacturers can utilize this tool to comb through historical data and pinpoint common trends and patterns that lead to recurring issues. Digital Twin Technology also can create countless simulations and what-if scenarios to predict their outcomes. Suppose a Manufacturer is thinking about changing out equipment, implementing a different process, or adjusting specific configuration settings. They can now predict the outcome of those changes to gain insight on the impact downstream. This ultimately leads to less selection bias and more data-backed decision making, which means more accurate and efficient manufacturing practices.
Real-time Monitoring
Digital Twin Technology acts as your omnipresent guardian on the Manufacturing line. It can keep a vigilant eye on the entire production process for you 24/7. Machinery Health and Performance are monitored to avoid any unplanned failures and downtime. Predictive maintenance strategies are devised and ready when the time comes for machinery to be replaced or fixed. If it detects any potential deviations or anomalies, it can send out an alert to notify the user. A manufacturer can be anywhere in the world, but still have access to key insights for ongoing processes in real-time.
Remote Access
A Manufacturer can access remotely the virtual representation of their Production line from anywhere in the world. Busy investors who don’t have time to visit a factory physically can now view it remotely, via Digital Twin Technology. With a visual representation that can be shown to anyone, anywhere, at any time, communication is strengthened.
Sustainability
Digital Twin Technology can help with reducing waste and minimizing energy consumption. It will analyse historical data and real-time processes to identify any unnecessary energy expenditures as well as provide waste reduction strategies tailored to your specific factory setup. It can assess potential changes in the production process for future impacts to the environment. Moreover, Digital Twin can help a Manufacturer stay compliant with environmental regulations by scanning production for any red flags.
With this heroic tool, not only would you be saving money, you’ll also be saving the environment!
Supply Chain Optimization
Supply chain logistics are important factors in successful manufacturing. Digital Twin Technology offers a Manufacturer the ability to monitor inventory accurately, as well as identify market patterns to make product demand forecasts. It offers tailored solutions to specific problems, by running simulations to predict various external and internal scenarios impacting supply chain logistics. For example, suppose a supply shipping route is closed. The technology can help you make an accurate data-backed decision on alternative route options, yielding the quickest transportation.
Are you ready to become A Hero of the Manufacturing Industry?
In the realm of manufacturing, the concept of Digital Twin Technology has emerged from the shadows as a heroic game-changer, revolutionizing how we design, simulate, and optimize production processes. As we delve into the intricacies of Digital Twin Manufacturing, we uncover a realm of possibilities that can reshape industries for the better.
However, these innovations must also align with regulatory standards and quality assurance. Process Validation takes center stage, ensuring that the Digital Twin's outputs are not only accurate, but reliable and consistent. In the battlefield of Manufacturing, Compliance Group, Inc stands as a beacon of hope. With a deep understanding of both the manufacturing domain and regulatory complexities, we offer tailored solutions to validate Digital Twin processes. From sensitivity assessments to uncertainty evaluations, our comprehensive services ensure your Digital Twin Manufacturing journey is not just innovative, but compliant and trustworthy.
CG's industry-leading expertise seamlessly bridges the gap between innovation and regulatory compliance. Are you ready to become a superhero? Reach out to us at sales@complianceg.com, and unlock the potential to harness your Digital Twin models with unwavering confidence.
FAQ's
Will Digital Twin Technology need to be validated?
This technology is still subject to compliance with regulatory standards and requirements. All information collected by this technology will have to be validated to ensure accuracy and privacy. Data from Machines, production processes, configurations, parameters, and other metrics will have to be displayed accurately in the Digital Twin. False data can yield incorrect data analytics and predictive insights.
What challenges are associated with implementing Digital Twin Technology?
The main challenge with implementing Digital Twin Technology is integrating it with existing systems such as ERP or MES. Implementation requires careful planning and execution. There is a steep startup cost to using Digital Twin Technology, but in the long-term, it can end up saving money for a company.
Another concern is data security. Whenever information on physical assets is collected and analysed as data, it’s important that this data is secured from a breach.
The System itself requires a strong network connection to function optimally, so areas with weak Wi-Fi or network infrastructure would most likely not be suitable for this technology.
Is Digital Twin Technology only for large-scale Manufacturing companies?
No! Digital Twin Technology is scalable and can easily be implemented into small production facilities as well as larger ones. It can be tailored to unique processes benefiting both large and smaller companies.
How difficult is it for non-tech savvy people to use this technology?
Although implementation of Digital Twin Technology systems would require a team of experts, the actual interface and navigation of the system is designed to be user friendly. This allows for just about anyone on the team to virtually access the analytics and layout of production processes.
What is Digital Twin Manufacturing, and how does it relate to maintaining the validated state?
Digital Twin Manufacturing involves creating a virtual replica of physical manufacturing systems and processes. It allows manufacturers to simulate, monitor, and optimize production in real-time. Maintaining the validated state refers to ensuring that manufacturing processes and systems consistently meet regulatory requirements and quality standards. Digital Twin Manufacturing helps achieve this by providing real-time insights and predictive analytics.
How does Digital Twin Manufacturing contribute to regulatory compliance in manufacturing industries?
Digital Twin Manufacturing provides a platform for continuous monitoring, analysis, and optimization of manufacturing processes. By integrating with quality management systems and regulatory requirements, it enables manufacturers to maintain compliance with regulations such as FDA 21 CFR Part 11 and ensures adherence to quality standards like Good Manufacturing Practices (GMP).
What are the key components of a Digital Twin in the context of manufacturing?
The key components of a Digital Twin in manufacturing include virtual models of equipment, production lines, facilities, and supply chains. These models are integrated with real-time data streams from sensors, IoT devices, and production systems to simulate and optimize manufacturing processes.
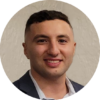
AUTHOR:
Manhal Chehayber
Validation Systems Analyst