Document Management Tips for Medical Device Companies
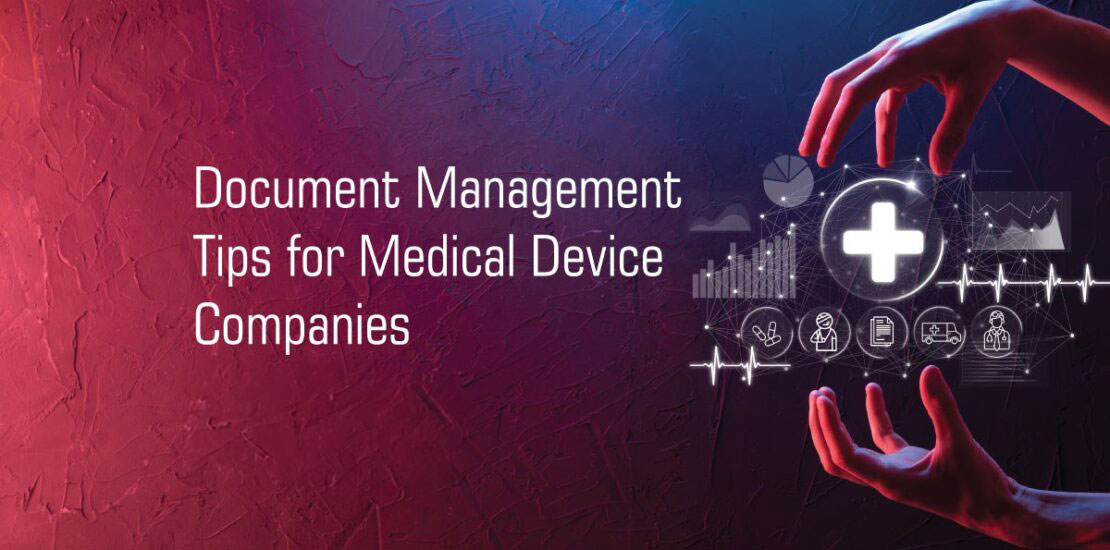
Article Context:
Documents and records prove that the company procedures align with compliance and regulation practices while designing, developing, and managing the life sciences products. It is a systematic process of classifying, strong, and retrieving documents with a predefined workflow streamlining the company practices to find information quickly and use the documents effectively, improving the operational performance and regulation practices. For example, for medical device companies, organizing documents and specific information regarding device designs, development processes, manufacturing techniques, procedures, and deviations forms a vital part of the device creation and marketing process. Without that documented information, the company lacks proof of its alignment with FDA (Food and Drug Administration) and ISO (International Standards Organization) regulations.
So, from simple procedures to critical design prototypes, document management in a medical device manufacturing company is vital. It is time-consuming to streamline the design development process and compliance. The documentation involves confidential information and strict regulations. However, document management is way beyond paper-based files management. It doesn’t’ mean the simple organization of paper documents. The company requires a solid, intelligent Document Management System like Document Management Software to manage, track and organize the complete document life cycle supporting the 21 CFR (Code of Federal Regulations) Part 11 and Part 820 regulations.
Compliance Group, an industry-leading quality management systems provider, has helped life sciences companies to move to electronic quality and document management from paper-based systems. As a result, we have developed a list of document management best practices for medical device companies. Unfortunately, the lack of a proper document leads to a compliance violation.
Develop a strategy and document the information
The FDA and other regulatory aspects consider the document as the primary object of evidence of the activities and procedures followed in the device creation. Therefore, if the development or manufacturing process lacks documentation or is not accessible during audits, the device creation process is not compliant.
Start to organize the documents at the earliest. Segment and segregate the documents to maintain a uniform filling system across the organization and save time while retrieving the documents.
With DMS, the organization can configure metadata fields and folders to create and manage documents efficiently. Create documents under predefined fields, segregate them into folders, process through defined workflow states with e-signatures and audit trails. Allows to Archive the documents that are no longer in use and avoid confusion for the employees to focus on the effective documents.
Here is a list of documents category the medical device companies segregate their documents
- Medical Device Design Prototypes
- Device History Records
- Non-Conformances
- CAPA’s
- Change Control Documents
- Customer Complaints
Go Digital and Stop using paper
DMS can configure and automate the document control processes following the standards and regulations. Strategically define workflows and approval process with e-signature. Track the signed and rejected documents to mitigate risk and prove that the authorized users have reviewed and signed, agreeing to the procedures and processes followed. It isn’t easy when companies follow paper-based approaches.
DMS allows easy collaboration on documents, tracks the changes made by the users, reviewers, and approver’s comments. Also, increased security with compliant e-signatures and non-editable audit trails captures the minute details of users with timestamps, documents and attaches the supportive documents of the design and manufacturing process. The multi-tab view helps the user segregate the information and quickly input data to store the documents in folders and files, allowing working on the current and latest versions and securing the previous and outdated versions for easy retrieval during audits and inspections.
Leverage could storage
With a broader range of documents in medical device companies, it is better to secure and store them on the cloud. In addition, the organizations can limit and delimit the accessibility of documents to users based on relevant role-based permissions for them to access the documents anytime and work collaboratively.
Centralize Documents Management System and Connect with Quality Management System
Apart from compliance and regulations, document security and accessibility are vital for medical device companies. The documents like design prototypes, calibration points, manufacturing procedures, development processes should be quickly accessible to the authorized users. So, they can access the needed information when it matters most. Unfortunately, this is impossible with paper-based systems as searching the documents in files and cabinets or through files and folders in individual desktops is human-intensive and time-consuming. Having all the documents in one platform like DMS Software is invaluable because it streamlines its needs and information to thrive.
Additionally, when DMS integrates with QMS (Quality Management System), documents and record linking facility enables the CAPA (Corrective Action and Preventive Action) and NC (Non-Conformance) to get linked with the relevant change control documents and eases the employee’s work in finding similar patterns and relevant documents in one go. Likewise when using the search features of the system, the users can find what they need seamlessly, and thereby reducing human errors.
Take a step forward
Undoubtedly, implementing new methods to manage and control medical device documents takes time and effort. But it is never a poor investment to secure, store and collaborate the documents to help ensure the device methods and products meet applicable requirements and specifications.
To know more about the DMS, take a step forward towards digital document management system by emailing us at sales@complinaceg.com